
It is used between joints in foiled projects, and can also be used in lead came channels, placed against the heart before glass is inserted. In the thin dimension it is very flimsy and can be easily bent to follow contours across your panel. You will also find restrip by other manufacturer's names: Morton calls theirs "strong line", Running Rabbit calls theirs "cameliner", etc. It is a thin, about 1/64" thick, copper coated steel band about 3/32" wide.

The other new innovation is reinforcement strip, commonly called "ReStrip", which is Venture Tape's trademark name. It would take a metallurgist to explain why this is so, but it works. The combination produces a strip that is stronger than solder alone. But the braid wicks up solder and becomes very stiff when filled with solder. That is true for just a single copper wire of some diameter. Now I said earlier that copper wire added no strength. The braid is made from very fine, braided, tin coated copper wires. One is a copper braid that can be integrated into the joints in foiled work. Recent technology has brought us two new innovations in reinforcement. The horizontal shadow lines you see in old church windows at 12" to 18" intervals used one of these types of rebar. It is placed across the back of the panel on edge and soldered to the lead joints it crosses. The other form of rebar is a zinc coated steel bar, 1/8" thick, and 3/8" to 1/2" wide. Copper wires were soldered to the lead joints in the panel, and when the panel was placed in the frame, the copper wires were twisted around the copper pipe. The ends of the pipe were set into holes in the frame.

The circular structure of the pipe is strong enough to hold a panel flat. One is a copper pipe, 1/2" to 3/4" in diameter. Traditional reinforcement used what is called "rebar".

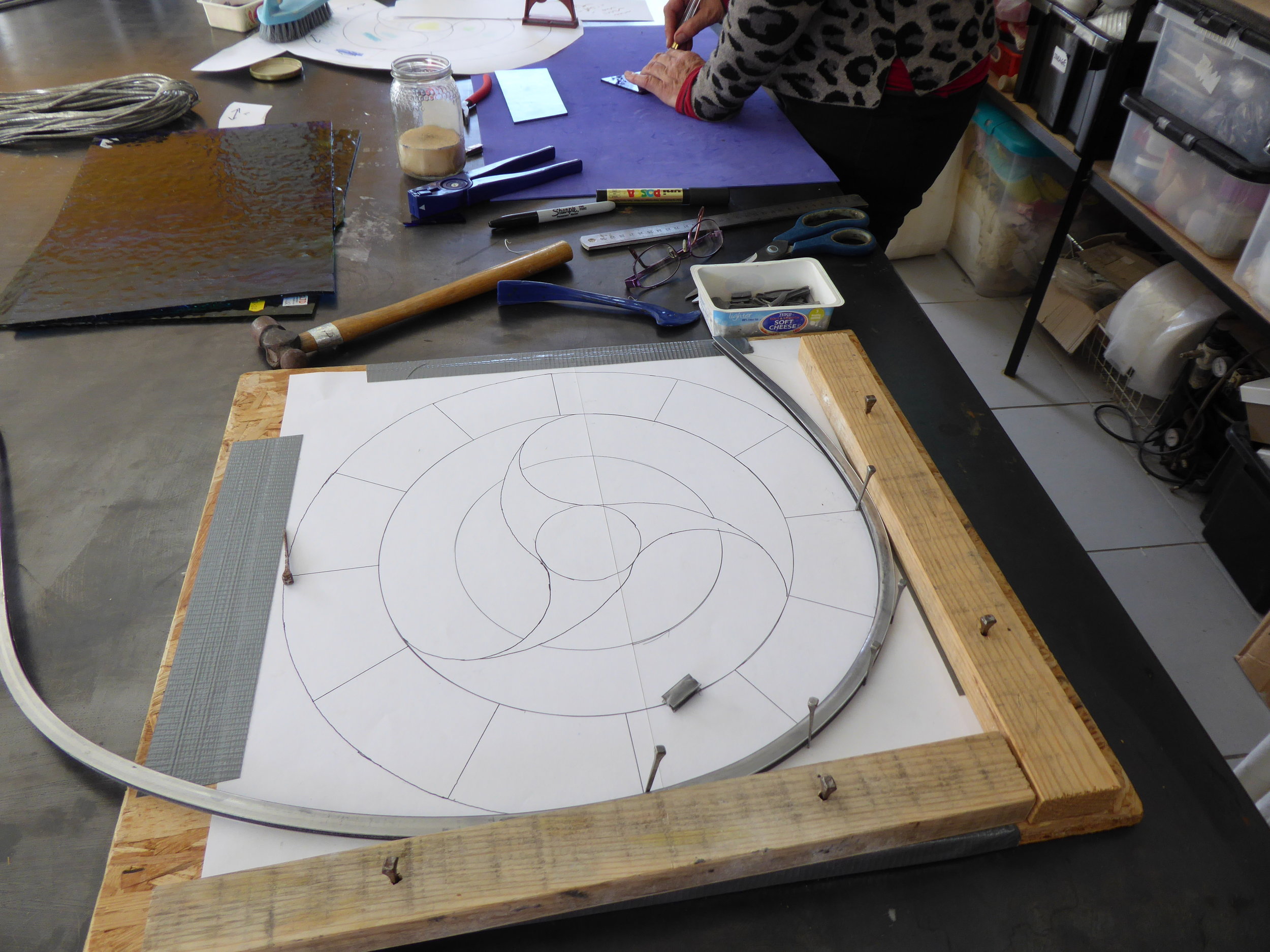
It has less strength than solder by itself, so a copper wire will do little to reinforce a panel. How do I reinforce a panel? Can I use copper wire?Ĭopper is a soft ductile metal and has little strength.
